TUCSON – The University of Arizona has partnered with a private manufacturing firm to create a more eco-friendly version of concrete.
Abraham Jalbout, CEO of Metoxs and Acrete, first approached Tech Launch at the University of Arizona with an idea to use leftovers from mining and coal plants for practical construction purposes.
“Abe came to us with all these great ideas, and Tech Launch decided to invest in them,” said Bob Sleeper, the licensing director for Tech Launch, which provides funding for inventions and startups.
The pair connected with professor Jinhong Zhang, who has researched construction materials created from waste for five years under a grant from the National Science Foundation.
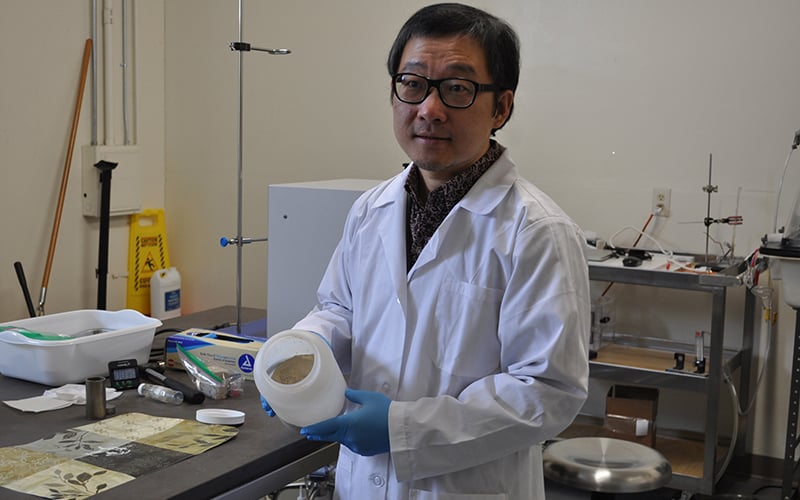
Junhong Zhang, a professor at the University of Arizona, has spent three years working with fly ash, a waste product from coal-burning power plants. (Photo by Courtney Kock/Cronkite News)
Zhang spent three years working with fly ash, a waste product from coal-burning power plants.
Fly ash is a fine, powdery material that used to be released into the air until the U.S. Environmental Protection Agency began requiring air filtering devices in coal plants in 2011. Physicians’ groups said the ash’s extremely fine texture can make it easier to inhale and lodge into the lungs, leaching heavy metals and other toxins into the body.
The team used that fly ash to create concrete they call Acrete, which they say is not only stronger than traditional concrete, but it also helps the environment.
“Fly ash is a problem all over the world,” Zhang said.
For example, Greenpeace studies have found that in China, many fly ash dumping points are not contained properly and are within a kilometer of villages, dairies and crops. Nearby residents complain of medical problems ranging from respiratory issues to reduced fertility.
“We’re definitely very … focused on environmental sustainability,” Jalbout said.
Traditional cement is typically made of limestone, sand and water.
Some traditional cement also uses fly ash, but the Acrete mixture is nearly 100 percent of the byproduct, Zhang said.
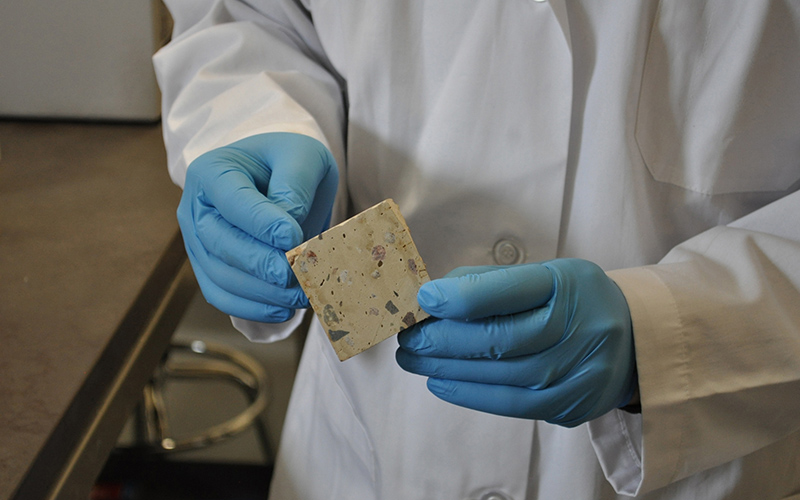
Zhang shows a hardened piece of Acrete. (Photo by Courtney Kock/Cronkite News)
Making cement also requires extreme temperatures.
According to the EPA, the cement manufacturing process is third-largest source of industrial pollution.
In the garage-sized lab, in a nondescript building 15 minutes east of the University of Arizona, Zhang mixed a small sample of Acrete in a beaker: no heat, no kiln, no giant rotating work truck. He used a hand mixer he said he purchased for less than $50.
Zhang said Acrete is much more resistant to water than typical concrete and is more than three times stronger. “It can sit in water for one month, two months, without changing in strength,” he said.
The Acrete team is pursuing a patent for their product, and they’re still exploring how to use mine tailings in construction materials.